Dans les coulisses d'une usine de production de robinets en Allemagne
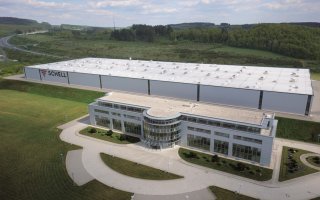
« Nous consommons 6 000 tonnes de laiton, italien et allemand, par an », souligne Jens Dohmann, directeur des exportations, en indiquant au fond de l'entrepôt le stock de barres en laiton.
Celles-ci sont tout d'abord découpées en tronçons, de manière automatisée, puis les pièces sont chauffées dans un four à gaz à 700°, avant de passer par deux sous une presse de 400 tonnes. La pièce est ensuite moulée avant d'être découpée : « toutes les chutes de laiton sont récupérées puis envoyées aux fournisseurs pour être fondues à nouveau », ce qui représente environ 40 % de pertes, précise Jens Dohmann.
Les pièces passent alors au lavage, avec de la soude et des petites billes d'inox puis sont rincées. Arrive enfin la phase de décolletage où les pièces sont usinées par creusement de la matière. Un joint Asag, « inventé par Schell et qui remplace le joint teflon », est positionné sur la pièce par un robot. Sur de petites séries, la mise en place de ce joint est en revanche réalisée à la main.
Robots et humains au coeur de la production
Si « environ 95 % de la production est semi-automatisée », l'entreprise souhaite en effet « garder l'humain au cœur de l'activité », explique Jens Dohmann. C'est pourquoi certains postes sont restés manuels, pour permettre notamment à du personnel en situation de handicap de continuer à travailler. D'autre part, les machines sont « parrainées », à raison de deux employés responsables par machine pour veiller à leur bon fonctionnement.
Une fois ce premier processus accompli, les pièces sont acheminées par camion dans la seconde usine pour les finitions. Trois robots s'occupent du ponçage des pièces, mais le polissage se fait aussi manuellement car le robot ne couvre pas 100 % de la pièce. Les pièces sont contrôlées puis placées à la main sur des cadres avant de passer dans une vingtaine de bains pour le chromage.
![]() | ![]() |
L'usine est certifiée Well Efficiency Labelling et Leed Leadership in Energy and Environmental Design. « En cas d'accident, nous disposons d'un grand bassin en sous sol pour stocker le chrome. Il est très important pour nous de protéger la réserve d'eau potable à proximité de nos usines », explique Jens Dohmann.
Plusieurs tests sont ensuite effectués pour s'assurer de la qualité du produit fini. Un laser vient enfin graver le nom de la marque sur le robinet qui est assemblé et emballé à la main.
« Nous employons 400 salariés sur les deux sites et vendons 15 millions de robinets chaque année », chiffre Jens Gebers, directeur marketing du groupe. Le groupe dispose aussi de nombreuses filiales dans le monde, en Pologne, Belgique, Inde et Hongrie. Depuis 2013, il est également implanté en France à Nice et se targue d'être « très connu en Alsace-Lorraine ».
Mais l'objectif du groupe est de conquérir toute la France, en devenant un acteur majeur sur le marché de la robinetterie temporisée et en déployant notamment son offre de robinets d’équerre.
« Le robinet d'équerre a plusieurs avantages. Il permet de sécuriser un point de puisage, diminuer sa consommation d’eau et sa facture, mais aussi parfaire son installation », souligne Jens Dohmann. « De plus, il peut être installé le dernier jour du chantier, ce qui permet d'éviter les vols, fréquents pour ce type d'équipements ».
Reste que l'utilisation de robinets d'arrêt dans les collectivités n 'est pas encore obligatoire en France, même si « fortement conseillée », selon Denis Delaunay, directeur commercial France. « Le CSTB milite pour isoler chaque point de puisage et certaines entreprises comme Bouygues commencent à comprendre l'intérêt du système pour éviter les désagréments et faciliter le travail de l'installateur », assure-t-il.
Mais le groupe est bien conscient qu'un gros travail de sensibilisation reste encore à faire.
Claire Thibault
© Schell