Les profilés PVC du groupe Veka composés à 25% de matière régénérée
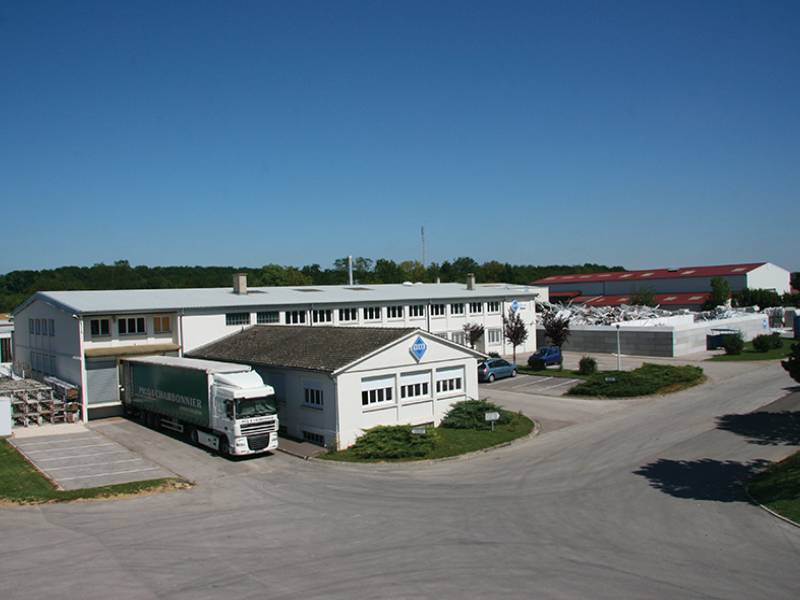
Le groupe Veka milite pour mobiliser la filière et les pouvoirs publics afin de collecter et de mettre en place un recyclage systématique des menuiseries PVC. Le fabricant estime en effet qu’il faut « interdire leur mise en décharge ».
Pour rappel, le PVC est 100% recyclable, « sans altération de ses qualités techniques ». L’intégration de matière R-PVC a également un impact moins important sur l’environnement. Utilisée en substitution de matière vierge, elle génère 17 fois moins de CO2 et consomme 9 fois moins d’énergie, détaille un communiqué.
A ce jour, Veka compte sur trois unités de recyclage en Europe (Allemagne, Royaume-Uni et France). Et ses capacités de co-extrusion ne cessent d’augmenter. Cet engagement du groupe en faveur de l’économie circulaire ne date pas d’hier puisque cela fait déjà 25 ans qu’il travaille au verdissement de son activité.
L’industriel explique : « Le recyclage des chutes de fabrication et des fenêtres en fin de vie s’effectue chez Veka depuis 1994 par l’intégration à cœur de ses matières dans les profilés. Une démarche innovante à l’époque, au départ sous suivi du CSTB. Depuis de nombreuses années, cet engagement voit sa qualité reconnue au travers des marques NF et QB et son intégration via les avis techniques (AT) et documents techniques d’application (DTA) de Veka ».
Veka, c’est aujourd’hui 25% de matière régénérée utilisée dans ses profilés, un taux que le groupe veut porter à 35% d’ici 2025.
L’exemple du site français Veka Recyclage
Implanté à Vendeuvre-sur-Barse (10) depuis 2008 sur un terrain de 30 000 m2, le site français Veka Recyclage est certifié QB34 (CSTB). Il s’approvisionne chaque année avec quelque 15 000 tonnes de menuiseries PVC en fin de vie. Autre source de matière, les chutes de production issues des fabricants de menuiseries Veka, dont le groupe assure la collecte. 5 000 tonnes/an proviennent ainsi de plus de 250 clients assembleurs, basés en France, Belgique, Pays-Bas, Portugal, Espagne et Italie.
A noter que le site français Veka Recyclage est ouvert à tous les fabricants assembleurs, quelle que soit l’origine des PVC collectés. En 2018, 20 000 tonnes de matière ont été recyclées et 22 000 tonnes sont prévues en 2019. Au global, le groupe recycle environ 80 000 tonnes de matière PVC par an.
Optimiser la collecte, le tri et le recyclage
En tant qu’extrudeur, Veka récupère ses déchets de production. Pour les fabricants de fenêtres, des « box » ou « bennes » sont mises à disposition sur les sites de fabrication puis acheminées vers Vendeuvre-sur-Barse. Pour les menuiseries en fin de vie, le processus est similaire : le collecte sur chantier est effectuée selon un cahier des charges précis. Des bennes sont mises à disposition pour récupérer tous les déchets PVC. Ce cahier des charges précise dans quelles conditions les déchets PVC seront acceptés et valorisés.
©Veka
Pour chacune des solutions, Veka délivre un certificat de recyclage permettant ainsi aux professionnels de la menuiserie de revendiquer la traçabilité de ces gisements évacués (selon directive EC 2020).
« La qualité du PVC, la qualité de tri ou de pré-tri ainsi que les volumes et les lieux sur lesquels les PVC seront collectés, induisent les conditions des coûts de traitement, via une procédure de suivi des entrées avec pesée, contrôle qualité et fiche de réception (…). Grâce à ce service chantier, Veka Recyclage a fait la démonstration qu’il était plus avantageux économiquement de faire appel à sa collecte, plutôt que de payer au prix fort, la mise en décharge d’un déchet PVC qui conserve, dans quelque état qu’il soit, une valeur marchande », souligne un communiqué.
Un processus automatisé de valorisation
Veka affiche 82% de valorisation des déchets PVC de menuiseries et de fermetures. Le processus de valorisation est automatisé : après différentes opérations de tris sélectifs des différents matériaux, la masse globale de la matière est broyée. Cisaillée et déchiquetée, elle passe au travers de cribles de différents calibres et subit une aspiration et un dépoussiérage.
Puis, un tri s’opère grâce à de puissants électro-aimants qui isolent la matière PVC des autres matériaux pour ensuite la faire transiter dans un immense tamis qui crible les fragments selon des critères dimensionnels (granulats de 4 à 15 mm). Puis, c’est au tour de l’extracteur de métaux d’entrer en action : grâce au courant de Foucaud, l’équipement intercepte trois familles de métaux non-ferreux comme l’aluminium, particules ferreuses et mélange mixte (PVC, Verre, Caoutchouc). Cette dernière passe dans une soufflerie, puis sur des tables vibrantes et subit une séparation pneumatique et électrostatique. Le PVC est enfin isolé !
©Veka
Veka procède aussi à la séparation ou dissociation du PVC blanc et des PVC teintés grâce à un dispositif de tri optique des couleurs. Une fois broyée, la matière régénérée est homogénéisée, extrudée et contrôlée en laboratoire. Des essais sont réalisés permettant de renseigner l’extrudeur client. Ils sont obligatoires dans le cadre de la marque QB 34 « Composition vinylique et sa fabrication pour profilés de fenêtres PVC » pour la production des matières recyclées, et de la marque NF 126 « Profilés de fenêtres en PVC ».
Puis, la matière régénérée est acheminée chez Veka pour être utilisée dans la fabrication de nouveaux profilés PVC. Veka explique : « Il est nécessaire que la matière régénérée s’extrude sans contrainte et ait des propriétés mécaniques proches de celles des matières vierges ». Sa qualité est une priorité « absolue ». Pour rappel, la co-extrusion permet de combiner différentes matières PVC pour réaliser le cœur et l’enveloppe extérieur du profilé.
A ce jour, 70% des matières retraitées par Veka le sont dans les produits de la fenêtre et les composants périphériques. « Les prochains enjeux se situent désormais autour de l’approvisionnement de matière à recycler », insiste Veka.
R.C
Photo de une : ©Veka