Siniat, une marque responsable et durable pour la construction d’aujourd’hui et demain
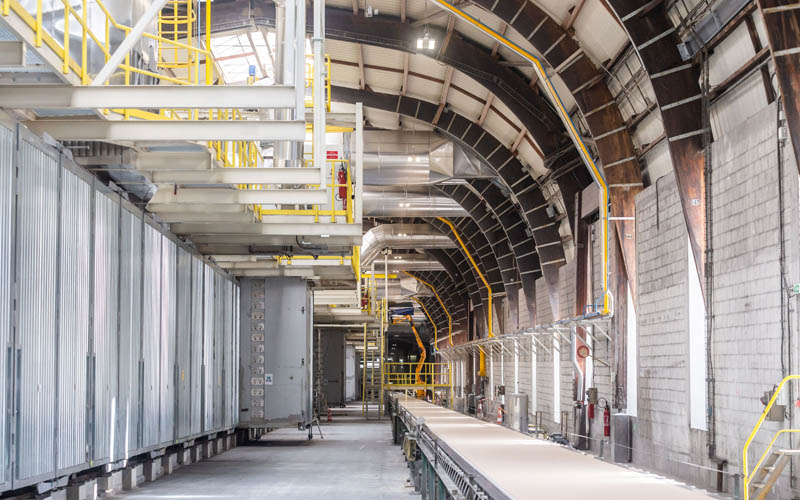
L’entreprise innove en permanence pour améliorer l’ensemble de ses équipements, installations et outils de production et chaque site industriel Siniat en est l’exemple concret.
![]() |
Mise en place du projet écoenergy à Auneuil
Sur son site d’Auneuil, situé dans les Hauts de France au sud de Beauvais, Siniat a engagé dès 2020 un projet ambitieux pour réduire sa consommation d’énergie et limiter son empreinte carbone. Ainsi a été élaboré le projet EcoENerGy, une véritable petite révolution industrielle permettant à Siniat de s’adapter avec succès à l’inflation, aux tensions sur le marché de l’énergie et aux enjeux environnementaux.
Avec un investissement de près de 30 millions d’euros, le site d’Auneuil tend à prouver qu’une production plus durable est possible.
Le projet EcoENerGy s’appuie sur 3 volets :
- Eco comme Ecologie,
- Ener comme Energie,
- Gy comme Gypse.
Eco comme Ecologie
En novembre 2022, Siniat a mis sa production à l’arrêt pendant 3 mois pour changer son imposant séchoir. D’une longueur de 200 mètres pour 8 mètres de hauteur, il datait d’une cinquantaine d’années et représentait environ 60 % de la consommation énergétique du site.
Cet ancien équipement a été remplacé par un séchoir nouvelle génération. Mis en service début 2023, il réduit de 20 % la consommation de gaz de l’usine, tandis qu’il augmente la vitesse de séchage, et donc la productivité de 10 %. Produire davantage en consommant moins d’énergie devient ainsi une réalité.
Le changement du séchoir a nécessité un investissement de 15 millions d’euros (soutenu à hauteur de 4,6 millions d’euros par l’État via le plan France Relance).
Au total, ce sont 5 900 tonnes de CO2 évitées chaque année, soit 20 % des émissions actuelles du site.
Ener comme Energie
Une énergie renouvelable et surtout locale !
À l’horizon 2026, la mise en place du nouveau séchoir sera prolongée de l’installation, par un partenaire, d’une nouvelle chaudière à énergie thermique à proximité de l’usine d’Auneuil. Ce combustible proviendra des filières locales de valorisation des déchets ou des matières biosourcées renouvelables provenant elles aussi de la région. Ce projet de chaudière à énergie thermique est en attente de validation de la subvention de l’ADEME.
L’utilisation de cette énergie thermique alternative et renouvelable permettra à Siniat de réduire encore de 60 % les émissions de CO2 et diminuera au total de 80 % la consommation de gaz du séchoir.
![]() |
Gy comme Gypse
Le site d’Auneuil consomme près d’un demi million de tonnes de gypse naturel par an provenant de deux carrières : la carrière de Montmorency située à environ 70 km et la carrière de Le Pin située à une centaine de kilomètres.
Grâce aux produits plâtres recyclables à l’infini, la matière recyclée utilisée aujourd’hui à Auneuil représente 15 % et provient essentiellement des déchets des chantiers et des rebuts de production. Siniat veut aller plus loin et intégrer jusqu’à 30 % de gypse recyclé dans la fabrication de ses plaques. Pour ce faire, l’industriel a conclu un partenariat avec une entreprise spécialisée dans la collecte et le recyclage. Ce partenaire s’installera dès 2024 sur le site d’Auneuil ce qui permettra également de réduire le CO2 émis par le transport, soit plus de 4 000 camions par an.
Le projet EcoENerGy sur le site d’Auneuil, n’est pas l’unique action mise en place par le site d’Auneuil. De nombreuses actions sont déployées pour préserver les ressources en eau.
Par exemple :
- le changement de la technologie du mixeur dès 2018 pour diminuer de 5 % la consommation d’eau.
- la récupération d’eau de pluie depuis quelques années. Avec une pluviométrie évaluée à 700 mm par an, Siniat peut ainsi récupérer jusqu’à 50 000 m3 d’eau par an. L’eau est stockée dans deux bassins d’une capacité de 12 000 m3. Puis elle est filtrée et intégrée dans la production.
En parrallèle du projet EcoENerGy, le site d’Auneuil comprend également des initiatives diverses pour réduire encore davantage l’empreinte carbone telles que :
- la sélection de transporteurs routiers selon leurs engagements à réduire leur consommation de gazole (140 camions partent chaque jour de l’usine),
- un parc de chariots élévateurs 100 % électrique,
- des livraisons à moins de 200 km,
- l’utilisation de carton recyclé pour la fabrication des plaques de plâtre,
- le passage au tout éclairage led.
![]() | ![]() |