Nouvelle usine de Prémurs à Vernouillet (28) : KP1, un acteur du bâtiment engagé dans l’économie locale
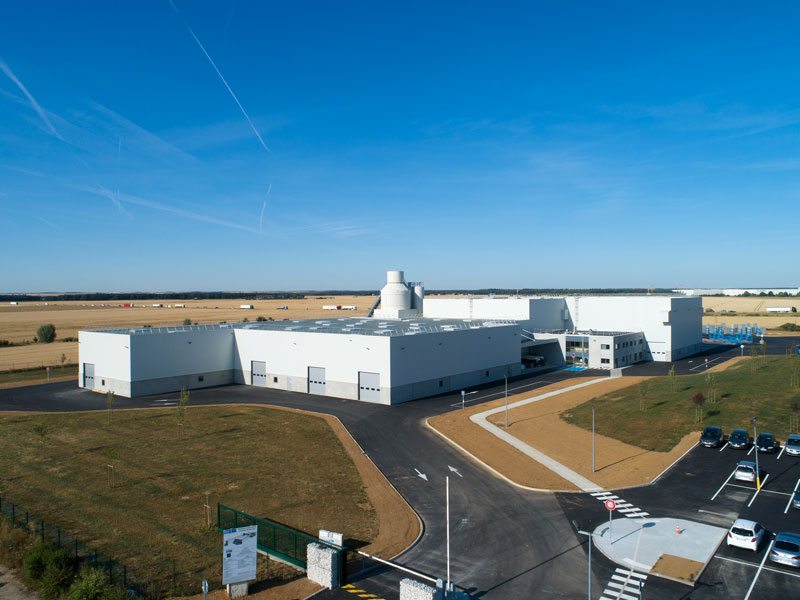
Un investissement de 15 millions d'euros qui porte à 21 le nombre total de sites de production. Située aux portes de l'Île-de-France, cette usine KP1 de 7 000 m2, la 3ème en périphérie de Paris, intègre une unité semi-automatisée de fabrication de Prémurs, une unité autonome de transformation des aciers et un bureau logistique. Elle produira près de 4 000 m2 de prémurs par semaine afin de fournir les chantiers du Grand Paris et des Jeux Olympiques d'été 2024. Elle permettra ainsi d'approvisionner rapidement et avec un impact environnemental minime tous les chantiers franciliens de logements, gares, infrastructures sportives et municipales...
Des équipements à la pointe
Tous les équipements de l'usine ont été sélectionnés avec soin pour optimiser la sécurité et l'ergonomie de chaque salarié, et la qualité des produits fabriqués. Innovant et gage de confort, le « poste de retournement » réduit au minimum les manutentions. Le système d'étuvage, le premier installé en France dans en process Prémurs, a également été choisi pour sa maîtrise automatisée de la température et de l'hygrométrie. Un dispositif qui garantit une planéité et une teinte homogène du parement du prémur. Des audits de contrôles ont été menés par KP1 tout au long de la conduite du projet. Une méthode d'accompagnement qui est allée au-delà de la conformité CE des machines* dans un objectif de réception sans réserve.
Une usine créatrice d'emplois
D'ici 2020, 52 emplois en CDI seront créés. Les profils recherchés sont diversifiés : conducteurs de machines, agents de préfabrication, pontiers, centraliers, techniciens de maintenance, techniciens de laboratoire, agents logistiques... La volonté du groupe KP1 est de recruter prioritairement des talents issus de la région Eure-et-Loir afin de dynamiser l'emploi local. Tous suivront une formation d'intégration ainsi qu'un stage opérateur.
![]() | Pourquoi le prémur KP1 ? |
* Audits des analyses des risques de conception chez les fabricants, audits des notes de calculs de fiabilité des équipements, audits des équipements sur plans 3D et audits sur site pour conformité dans l'environnement.
Une usine « made in KP1 »
KP1 BÂTIMENTS a réalisé la structure béton de l'ouvrage en mettant en œuvre l'ensemble des solutions KP1 fabriquées à proximité dans les usines de Limay (78) et Poincy (77) :
- près de 4 000 ml de poteaux et poutres pour la charpente,
- 600 m2 de prémurs pour les façades,
- 550 m2 de dalles alvéolées et 500 m2 de prédalles et ThermoPrédalles® pour les planchers des espaces bureaux et locaux sociaux
![]() |
La structure du bâtiment terminée, KP1 a intégré l'unité semi-automatisée de fabrication de prémurs, l'unité autonome de transformation des aciers et le bureau logistique. Le carrousel de production, la centrale à béton, et les machines de transformation du béton et du béton armé ont lancé les premiers tests de fabrication dès mai dernier. En parallèle, le centre d'essai KP1 de Pujaut (30) a mis au point la formulation béton. Les techniciens ont mis en place le parc informatique et ont innové avec l'installation de bornes de contrôle tactiles, un des exemples de la digitalisation de l'usine.
![]() | « KP1 BÂTIMENTS a joué un rôle central tout au long du projet. La clé du projet était de concevoir notre structure autour du process. Le BIM nous a permis d'optimiser notre charpente béton et d'intégrer l'ensemble des équipements industriels. La relation entre notre service Étude de prix et Hugues PHILIPPE, Ingénieur KP1 en charge de la construction de l'usine de Vernouillet, a été primordiale. |
Après la finalisation de notre offre commerciale, notre bureau d'études a pris le relais afin de réaliser toutes les notes de calculs et plans d'exécutions. Pour la pose de la charpente béton et des panneaux de soubassements, il aura fallu compter six semaines de réalisation. », explique Aymeric VINCENT, Chargé d'affaires KP1 BÂTIMENTS.
Les étapes de fabrication d'un prémur
Étape 1 : le coffrage
Avant d'installer les règles pour le coffrage, un système de brosses nettoie les tables provenant de la dernière étape « évacuation » puis une huileuse automatique les graisse pour faciliter dans un second temps le décoffrage. Le robot de coffrage place ensuite les règles numérotées aimantées selon les plans définis en amont. Une zone manuelle permet d'achever les coffrages avec du polystyrène et de positionner précisément tous les inserts (douilles, réservations, pots électriques...) grâce à deux lasers. | ![]() |
En bord de ligne, l'atelier de menuiseries prépare les mannequins de coffrage. Une redresseuse découpe ensuite les aciers et met en place automatiquement les cales d'enrobage. Pour terminer, les armatures sont mises en place sur la table par l'opérateur.
Étape 2 : le ferraillage
Dans le hall d'armature, les aciers « béton armé » arrivent en bobines. Deux lignes de ferraillages sont installées pour optimiser les flux de production. Une machine découpe automatiquement et à la demande les raidisseurs. Ils sont ensuite stockés par hauteurs et gammes. Une cadreuse et un atelier de ferraillage de cage d'armature sont dédiés aux renforts, linteaux, poutres voiles... | ![]() |
Étape 3 : le coulage
La table avec coffrage et ferraillage se place au niveau du malaxeur pour le dosage et la dépose automatique du béton. Cette zone est totalement close pour une sécurité accrue. Une fois le béton coulé, la table lance les vibrations afin d'obtenir une surface homogène et plane. Le malaxeur possède une capacité de 1 m3 et une production maximale de 15 m3/heure. | ![]() |
Toute la gestion est automatisée et gérée depuis ce poste. La zone de coulage possède un accès direct vers l'étuve pour les faces « 1 » des prémurs tandis que les faces « 2 » se dirigent directement vers l'étape « retournement ».
Le béton est réalisé sur place. L'usine possède deux silos de ciment et un silo filaire de 70 tonnes chacun. Quatre compartiments à agrégats - deux de sables et deux de granulats de 130 tonnes chacun - complètent le dispositif. Un système séparateur retraite également les déchets. Une vis sans fin extrait les granulats pour les recycler. | ![]() |
L'eau de lavage est également placée dans un bassin de décantation. Après correction du pH, elle est renvoyée dans le circuit d'eau usée collectif.
Étape 4 : le retournement
Ce poste permet d'assembler automatiquement les deux faces d'un prémur. Afin de renforcer l'ergonomie et la sécurité des salariés, KP1 a installé une machine innovante. Les éclisses, de 18 à 30 kg, sont désormais solidaires du retourneur. Les opérateurs n'ont plus à les porter. Ils les font uniquement glisser, réduisant ainsi les charges manutentionnées dans la journée.
L'étuve peut accueillir 48 prémurs en simultané sur quatre colonnes. Le temps de séchage moyen dans cette enceinte est de 8 heures pour atteindre 20 Mpa. KP1 a sélectionné une machine inédite en France, qui combine la maîtrise de la température et de l'hygrométrie. Des canaux d'approvisionnement de l'air chaud et un générateur de vapeur assurent un séchage homogène. Ce dispositif permet d'obtenir une planéité et une teinte homogène du parement du prémur.
![]() |
Étape 5 : l'évacuation
Le hall d'évacuation est équipé de deux ponts roulants de 6,3 tonnes qui permettent de déplacer à l'extérieur les prémurs pouvant atteindre 12 tonnes. Une table relevante et neuf emplacements de rack assurent la mise en place sur les camions. 15 à 20 livraisons sont organisées chaque jour.
Le plus :
KP1 possède deux différents types de camions. L'un standard de 9 mètres de longueur et le second de 6 mètres, développé exclusivement par et pour l'entreprise afin de livrer avec aisance les chantiers parisiens difficiles d'accès.