Transformable et transportable, un collège construit à la mode industrielle à Clisson
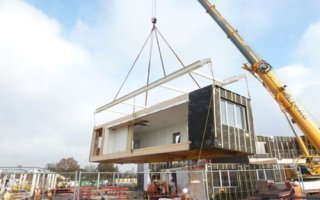
Lorsqu'il s'agit de mettre un nom sur sa fonction, Xavier Jaffray, dirigeant de l'entreprise Leco XJ, peine parfois à trouver les mots tant celle-ci est encore peu commune dans le secteur. « Assembleur industriel » demeure pour l'heure, le meilleur compromis qu'il ait trouvé afin de résumer sa mission : « développer les process d'assemblage associés à des modes constructifs dans le but de diminuer les coûts de construction et d'améliorer les performances qualité et conditions de travail.» Clisson, en Loire Atlantique, en mesure actuellement les bénéfices.
Située à la limite sud-est du Vignoble nantais, la commune profite en effet actuellement d'un système de construction semi-industrialisé innovant pour la réalisation de son second collège public, en modules de bois de grandes dimensions dont la gestion de fabrication a été confiée à Leco XJ. « Le maître d'ouvrage voulait de la construction modulaire pour que collège puisse être agrandi, diminué, assemblé. La réponse a été apportée par un groupement qui a sous-traité la partie construction et la partie assemblage modulaire », précise Xavier Jaffray.
Ainsi, 98 modules en bois dont le plus long mesure 16 mètres se transforment jour après jour en salles de classes dans un atelier éphémère situé à moins de trois kilomètres du site de construction du collège. « Il s'agit de l'une des particularités du chantier : tout se fait sur place » précise l'assembleur industriel avant de souligner l'intérêt économique de la démarche : « un industriel qui se déplacerait payerait les frais de transports .»
Main d’œuvre 100% locale
La seconde particularité réside dans le fait que la fabrication des modules en atelier fait appel à une « main d’œuvre 100% locale, en excluant les trois encadrants de Leco », poursuit Xavier Jaffray. « 30 ouvriers sont rentrés dans un processus de formation avant la production. Une semaine a été consacrée au gros œuvre (ossature bois) et une semaine pour le second œuvre.»
Ce dernier va jusqu'à parler de « cercle vertueux » pour qualifier sa rencontre avec les sept entreprises locales, dont MC France qui a fabriqué et fournit 136 ensembles de menuiseries. « Nous avons convaincu le maître d'ouvrage que notre solution de menuiseries mixtes bois-alu était en parfaite adéquation avec la démarche de haute qualité environnementale du projet, notamment en termes de performances, de durabilité et de solution techniques, comme la création d'une quincaillerie spécifiquement adaptée aux besoins de sécurité et de ventilation du bâtiment », indique Antoine Argentieri, directeur commercial de MC France.
Outre sa manière de travailler avec des acteurs locaux et son système breveté sous licence Dhomino, l’innovation du projet réside dans son modèle économique. « L'objectif est de bâtir un modèle économique qui soit une alternative économique et l'économie n'est pas dans le produit, donc dans le bois : elle se trouve dans le temps de pose qu'il faut rationaliser », assure le dirigeant de l'entreprise Leco XJ. « Ainsi, le temps qu'on a pu gagner en atelier compense les frais annexes.»
En moyenne, deux modules sont produits par jour. « Ce rythme a un coté assez violent par rapport à ce qui se fait habituellement sur chantier » concède Xavier Jaffray qui souligne que « cette démarche demande un sacré boulot de synthèse en amont.»
3000 m² dédiés à la logistique
Toujours dans l'optique d'optimiser les temps de pose, les matériaux livrés à l'atelier ne sont pas directement dirigés vers les postes de travail mais dispersés en lots par des caristes dans une zone dédiée de l'atelier de 15 000 m². « Sur un chantier ordinaire, on ne trouve jamais 3000 m² consacrés à la logistique comme ici. Ça représente un coût certes mais il est largement compensé par le temps de gagné sur les différents postes de travail », estime le dirigeant de Leco XJ
Une fois achevé, un module correspond à une demi-salle d’enseignement de 27 à 50 m² et est assemblé aux autres sur site, lorsque les travaux de finitions sont quasiment achevés. Seul le tronçon de circulation, c'est à dire le couloir qu'il intègre est également achevé sur place pour permettre les opérations d'assemblage et de connexion.
Pour l'instant, l'ouvrage de 5 767 m² est constitué de vingt divisions répondant aux normes d'isolation phonique et thermique. Mais au besoin, il sera possible d'en enlever ou d'en rajouter à souhait. Après douze mois de réalisation, contre dix-huit mois pour un collège traditionnel, les travaux devrait s'achever en février prochain pour une ouverture programmée à la rentrée 2015.
Audrey Le Guellec
© A. LG (Batiweb)