Girrasol un défi technologique en eau profonde
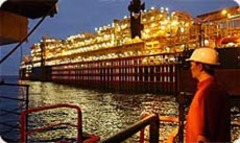
Le
forage par grands fonds
Les puits de Girassol ont été forés par deux bateaux de forage à positionnement dynamique. (Maintien d'un engin flottant en station, en particulier à la verticale d'un puits en mer, en opposant à la force de dérive la réaction conjuguée de propulseurs contrôlés par calculateurs.) Le Pride Africa et le Pride Angola, ont été construits spécialement pour l'exploration et le développement des champs du Bloc 17. Pour une plus grande stabilité, ils sont équipés de propulseurs à vitesse variable. Le forage a commencé fin juin 2000 avec le Pride Africa.
Les systèmes de production sous-marins
Les systèmes de production sous-marins (SPS) comprennent les manifolds* de production, les têtes de puits, les Christmas-tree** et les interconnexions puits/manifolds (well jumpers). Le schéma de développement du projet a nécessité le forage de 39 puits sous-marins associés au FPSO, à savoir 23 puits producteurs, 14 injecteurs d'eau et 2 injecteurs de gaz associé issu du traitement du brut. Pas moins de 13 manifolds sous-marins et leur système de contrôle associé ont été installés sur le fond de la mer.
Au total, 500 vannes gèrent la circulation des différents fluides entre les puits sous-marins et les installations de surface. Afin de maximiser la productivité et de réduire le nombre de puits à forer, on a utilisé la technique des puits horizontaux. Le débit de certains de ces 39 puits peut atteindre 35 000 b/j. Fabriquées en Norvège, les têtes de puits capables de supporter de très fortes pressions ont pour fonction de contrôler le débit de l'effluent en provenance du réservoir et de fermer le puits en cas de nécessité. Ces premiers équipements ont fait l'objet de nombreux tests lors de leur réception : tests en usine, tests en eau profonde à Bergen (Norvège). Chaque élément a en effet subi un contrôle très strict car, à plus de 1 000 mètres de profondeur, il est seulement possible de manoeuvrer la vanne à distance ou de faire intervenir un robot. Le moindre défaut demanderait de remonter toute la tête de puits, ce qui serait extrêmement coûteux. Les livraisons ont commencé en septembre 1999.
Le
système de conduites sous-marines
Les têtes de puits sont reliées au FPSO par un réseau de conduites sous-marines, la grande profondeur du champ imposant de tenir compte de la température.
Le problème de température est en effet crucial, étant donné que l'eau au fond est seulement à 4° C et qu'il est absolument nécessaire de maintenir le brut à plus de 40° C jusqu'à son arrivée en surface (notamment pour éviter la formation d'hydrates et le dépôts de paraffines). La température du brut est considérée comme peu élevée aux environs de 65° C à la sortie de la tête de puits et, si l'on utilisait de simples conduites en acier, elle chuterait rapidement (18° C par kilomètre « non isolé » parcouru) d'autant que la distance à parcourir dans les bundles peut atteindre 7 km auxquels il faut ajouter les 1 300 mètres de hauteur de la tour riser. Par ailleurs, dans la partie verticale, la thermodynamique du fluide entraîne une perte inévitable de 10° C. Il ne reste donc que 8° C de marge pour la partie horizontale : il est donc impératif de ne pas perdre plus de 1 degré par kilomètre parcouru. C'est pourquoi on a eu recours à un système d'isolation thermique de l'ensemble des équipements sous-marins principalement des conduites en utilisant un produit isolant apte à remplir simultanément trois conditions :
Isolation et inertie thermiques afin de maintenir la température constante pendant au moins 16 heures en cas d'arrêt Résistance à une pression de 140 bar Flottabilité (via la réduction de poids) On a pris le parti d'utiliser une mousse syntactique de haute densité, dont la capacité d'isolation est 500 fois supérieure à celle de l'acier
Les
tours risers: une innovation majeure
Ces structures élancées, d'une hauteur de 1 250 mètres, ont pour fonction de remonter les effluents depuis le fond de la mer jusqu'au FPSO. Leur conception a fait l'objet d'études détaillées et de tests en laboratoire (à Sartrouville, dans la banlieue parisienne) afin de vérifier les performances d'isolation thermique de la mousse syntactique incorporée. Les tours elles-mêmes ont été fabriquées en Angola, sur le chantier de Lobito, spécialement adapté pour la fabrication de ces structures.
Les tours risers sont l'une des innovations majeures du projet Girassol, elles comprennent chacune quatre lignes de production et deux lignes d'injection d'eau ou de gaz. Les lignes de production sont raccordées aux boucles de production et permettent l'introduction régulière dans le circuit de racleurs nettoyants chargés de dégager la paraffine qui pourrait se former sur les parois du tuyau et gêner l'écoulement du pétrole. En outre, chaque boucle de production comprend un tuyau qui peut éventuellement injecter du méthanol dans le circuit pour empêcher la formation d'hydrates. C'est en effet avec l'action du froid associé à l'eau que le gaz présent dans le pétrole forme de la glace (hydrate) susceptible de boucher les conduites. Par ailleurs, afin de maintenir la pression dans le gisement, de l'eau de mer est injectée en remplacement du brut extrait, et le gaz qui a été séparé du brut est réinjecté au lieu d'être brûlé, ce qui permet de limiter la production de gaz à effet de serre.
Pour mettre en place les tours risers, il a fallu remorquer ces 1 250 mètres de conduites depuis leur site de construction jusqu'à celui de leur destination finale sur le champ de Girassol. Il était indispensable qu'elles subissent le moins de sollicitations possible pendant le trajet en mer, et ce, malgré les courants et les vagues. L'itinéraire emprunté représente donc environ 600 km. Le remorquage de chaque riser n'a pris que cinq jours et leur mise en place qui pourtant constituait une « première » s'est effectuée en quelques heures. Arrivée sur site, chaque tour riser a été basculée au moyen d'un contrepoids. Le suivi permanent de ce basculement s'est opéré grâce à un ensemble de capteurs de position situés sur la tour riser, sa partie intérieure étant retenue dans sa descente par des lignes raccordées à des navires à positionnement dynamique. Une fois à la verticale et raccordée à une ancre à succion, la tour riser est maintenue grâce au flotteur de tête et à la flottabilité de la mousse syntactique.
* Ensemble de conduites et de vannes dirigeant l'effluent ou la production dans des installations.
** arbre de Noël, en anglais. Tête d'un puits de production. Ensemble de vannes, duses, appareils de contrôle et de mesure, en forme de croix, qui constitue la tête d'un puits éruptif en production et sert à contrôler son débit